MPulse CMMS Software
Compare Maintenance Software Editions
MPulse CMMS Software makes it your decision, not ours. Subscribe annually or own the software outright. Host it yourself or let us handle it for free. No matter your choice, you get the same powerful features and support.
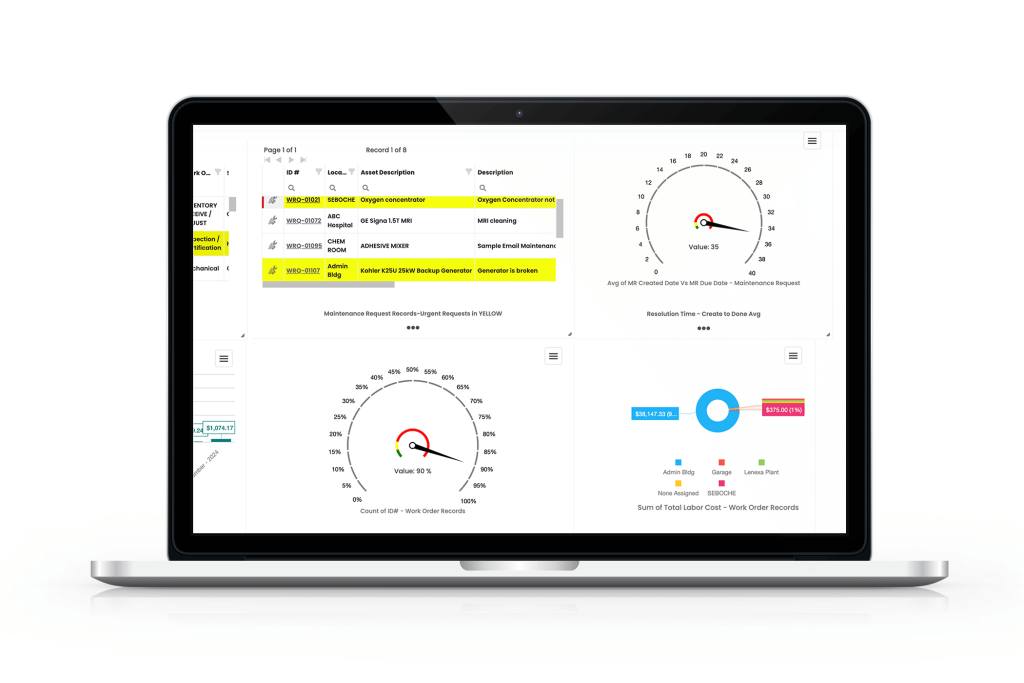
We’ve Designed a Flexible Family of Maintenance Management Products and Work Order Software that Scales With You and Your Team
MPulse CMMS offer three editions designed to fit the size and scope of your maintenance management requirements.
Professional
A full-featured CMMS for small to midsized organizations needing standard maintenance and repair functionality - more than "Basic" work order software.
Professional Edition Includes:
- Unlimited PM Scheduling & Tracking
- Unlimited Work Orders
- Free and Unlimited Maintenance Requesters
- Parts and Supplies Inventory Management
- Unlimited Dashboards with Calendars, Data Tables, and Graphical KPIs
- Powerful Analytics
- Real-Time Notifications
Advanced
Sophisticated asset management and CMMS features for managing complex maintenance operations, multiple locations, and large teams providing reliability centered maintenance.
Everything in Professional, plus:
- Unlimited Customizations to create custom forms and reports
- Condition Based Maintenance
- Unlimited Cumulative and Conditional meters
- Inventory Purchasing
- Automated Cycle Counts
- Role Based Record Access
- Asset Lifecycle Tracking
- Budgets and Cost Centers
- Unlimited Asset Status Boards
Enterprise
Our most robust edition includes premium features and is ready out of the box for Industrial Controls and IoT. Our most comprehensive maintenance CMMS. Ideal for large organizations.
Everything in Advanced, plus:
- Unlimited Cumulative and Conditional Meters
- Easy Integrations with Accounting Systems, Machine Data, and Smart Buildings
- Single Sign On
- 52 Week Resource Planning Board
- Resource Leveling
- Personnel Qualification Tracking
MPulse CMMS Makes Maintenance Operations
More Productive
MPulse CMMS provides reliable scheduling and tracking of planned and unplanned work orders, along with powerful analytical tools for equipment and facility maintenance organizations.
Loved by 3,500+ customers around the world
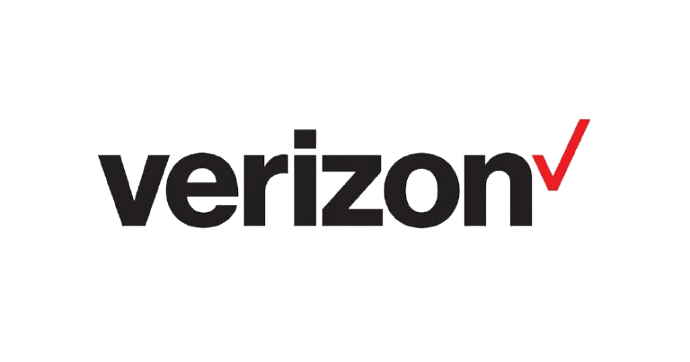
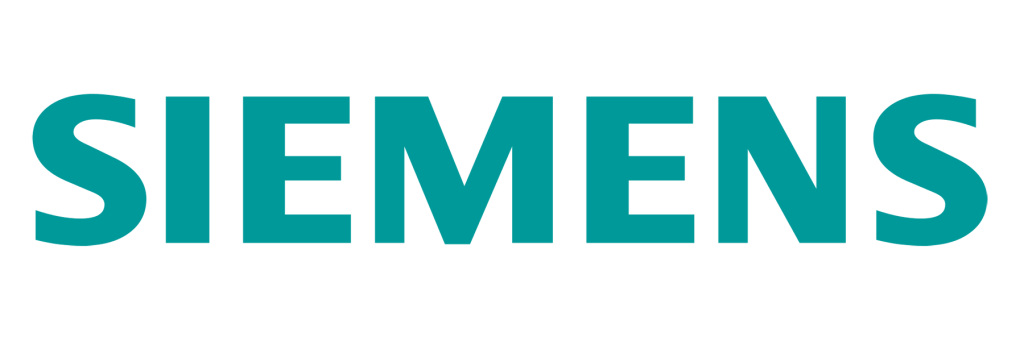
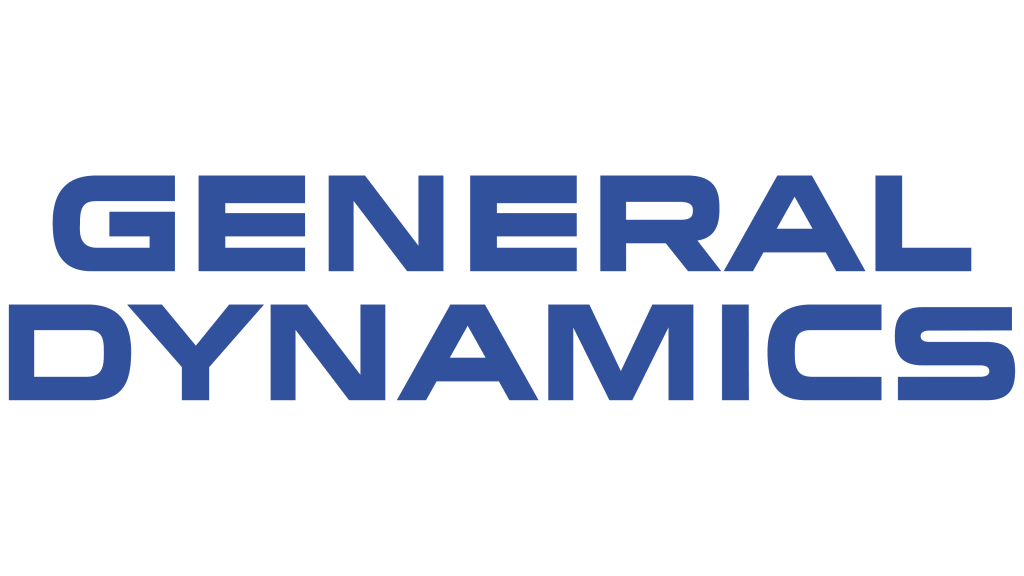
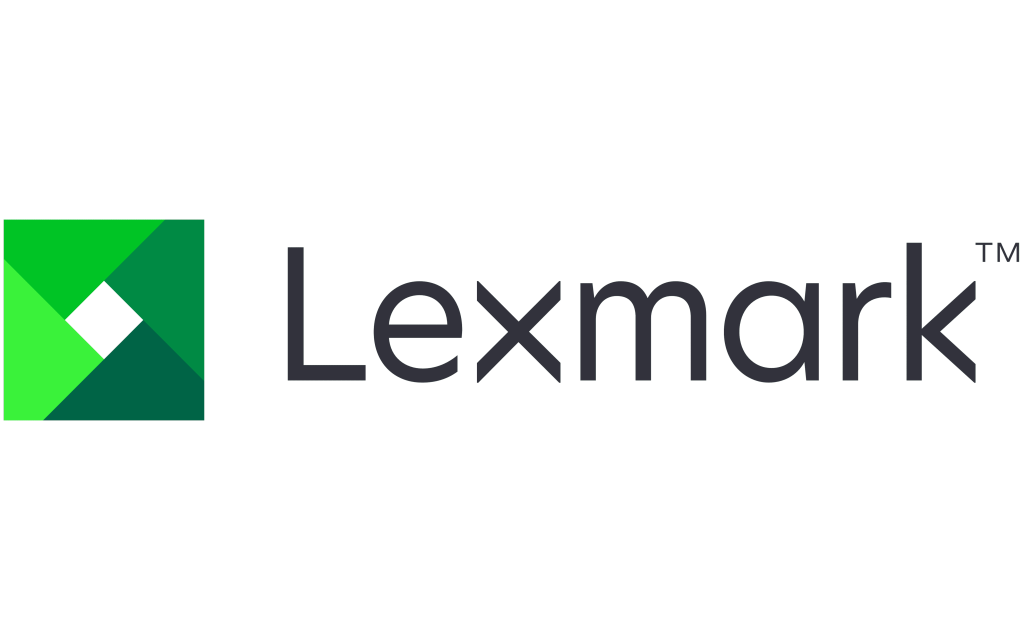
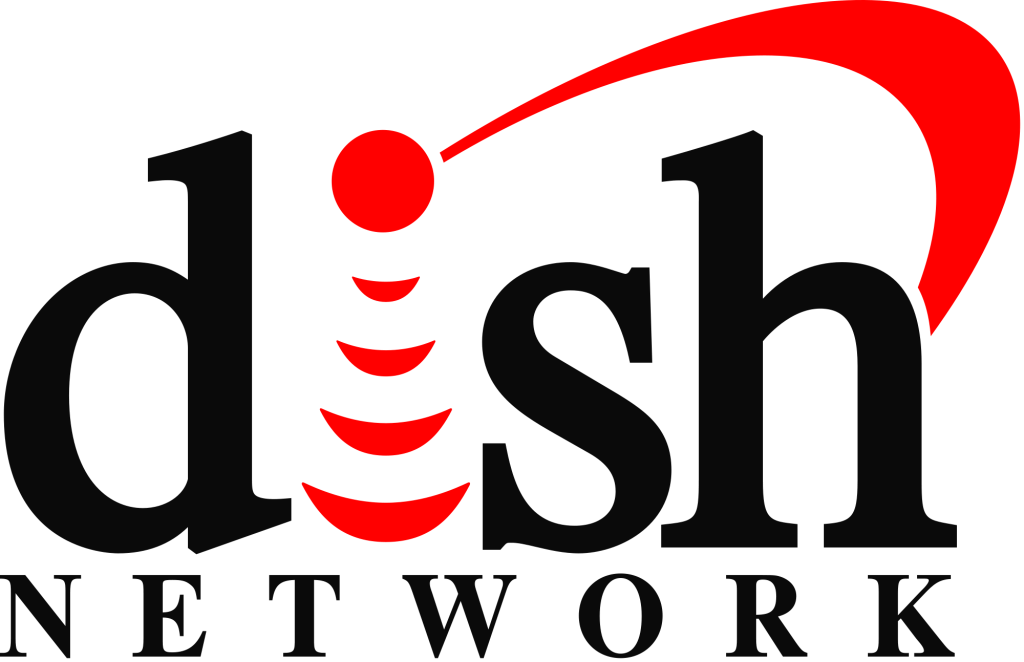
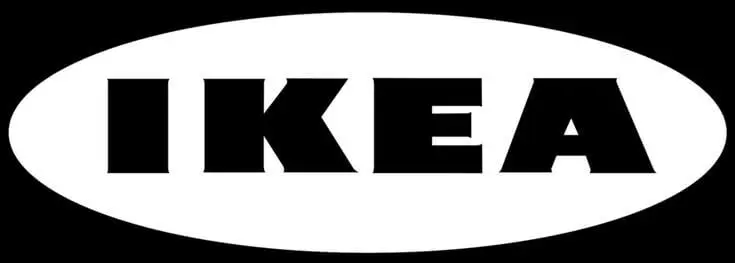
MPulse CMMS Software Features
Standard
|
Most Popular
|
||||||||||||||||||||||||||||||||||||||||||||||||||||||||||||||||||||||||||
---|---|---|---|---|---|---|---|---|---|---|---|---|---|---|---|---|---|---|---|---|---|---|---|---|---|---|---|---|---|---|---|---|---|---|---|---|---|---|---|---|---|---|---|---|---|---|---|---|---|---|---|---|---|---|---|---|---|---|---|---|---|---|---|---|---|---|---|---|---|---|---|---|---|---|---|
Work Orders |
Basic | Enhanced | Full Featured | ||||||||||||||||||||||||||||||||||||||||||||||||||||||||||||||||||||||||
|
|||||||||||||||||||||||||||||||||||||||||||||||||||||||||||||||||||||||||||
Maintenance And Repair Requests |
Basic | Enhanced | Full Featured | ||||||||||||||||||||||||||||||||||||||||||||||||||||||||||||||||||||||||
|
|||||||||||||||||||||||||||||||||||||||||||||||||||||||||||||||||||||||||||
Scheduled Maintenance (PM) |
Basic | Enhanced | Full Featured | ||||||||||||||||||||||||||||||||||||||||||||||||||||||||||||||||||||||||
| |||||||||||||||||||||||||||||||||||||||||||||||||||||||||||||||||||||||||||
Asset Management |
Basic | Enhanced | Full Featured | ||||||||||||||||||||||||||||||||||||||||||||||||||||||||||||||||||||||||
| |||||||||||||||||||||||||||||||||||||||||||||||||||||||||||||||||||||||||||
Parts Inventory Management |
Basic | Enhanced | Full Featured | ||||||||||||||||||||||||||||||||||||||||||||||||||||||||||||||||||||||||
| |||||||||||||||||||||||||||||||||||||||||||||||||||||||||||||||||||||||||||
Resource Planning |
Basic | Enhanced | Full Featured | ||||||||||||||||||||||||||||||||||||||||||||||||||||||||||||||||||||||||
| |||||||||||||||||||||||||||||||||||||||||||||||||||||||||||||||||||||||||||
Reporting And Analytics |
Basic | Enhanced | Full Featured | ||||||||||||||||||||||||||||||||||||||||||||||||||||||||||||||||||||||||
| |||||||||||||||||||||||||||||||||||||||||||||||||||||||||||||||||||||||||||
Data Integration |
Basic | Enhanced | Full Featured | ||||||||||||||||||||||||||||||||||||||||||||||||||||||||||||||||||||||||
| |||||||||||||||||||||||||||||||||||||||||||||||||||||||||||||||||||||||||||
Mobile Access |
Basic | Enhanced | Full Featured | ||||||||||||||||||||||||||||||||||||||||||||||||||||||||||||||||||||||||
| |||||||||||||||||||||||||||||||||||||||||||||||||||||||||||||||||||||||||||
Security And Administration |
Basic | Enhanced | Full Featured | ||||||||||||||||||||||||||||||||||||||||||||||||||||||||||||||||||||||||
| |||||||||||||||||||||||||||||||||||||||||||||||||||||||||||||||||||||||||||
Notifications |
Basic | Enhanced | Full Featured | ||||||||||||||||||||||||||||||||||||||||||||||||||||||||||||||||||||||||
| |||||||||||||||||||||||||||||||||||||||||||||||||||||||||||||||||||||||||||
Support |
Basic | Enhanced | Full Featured | ||||||||||||||||||||||||||||||||||||||||||||||||||||||||||||||||||||||||
|
MPulse Maintenance Software is
Perfect for any Industry
Our CMMS software provides solutions for all types of industries. From manufacturing to education, learn how MPulse can help you address your business’ challenges.
MPulse Means Happy Customers
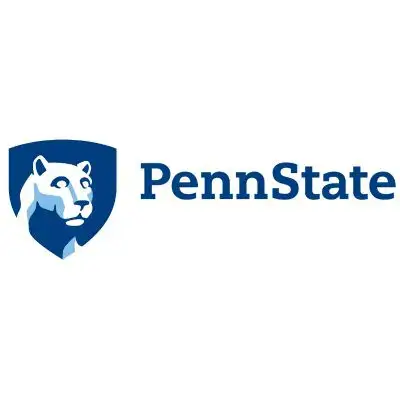
“The features and price made MPulse the right choice and the service has been excellent.”
John Smith
Maintenance Supervisor, Penn State University
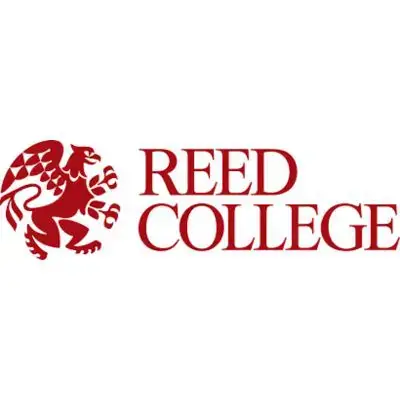
“You can tailor the program to fit the needs of your particular facility. The performance of the software is overall very good.”
Maintenance Manager
Reed College
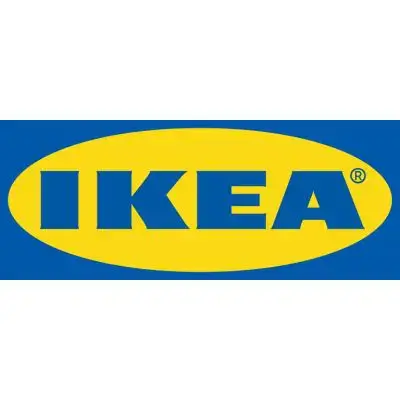
“I started using MPulse in March of 2006 using v6. The upgrade to v7 has been a smooth and easy transition offering more of the features that are needed by my sites.”
Facilities Manager
IKEA US West Inc.
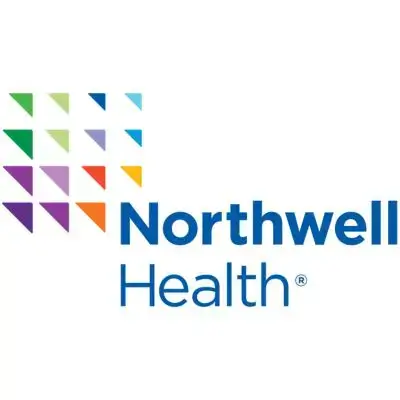
“It certainly has simplified keeping track of what we do and how we do it.”
Director of Engineering
Real Estate Services, Northwell Health
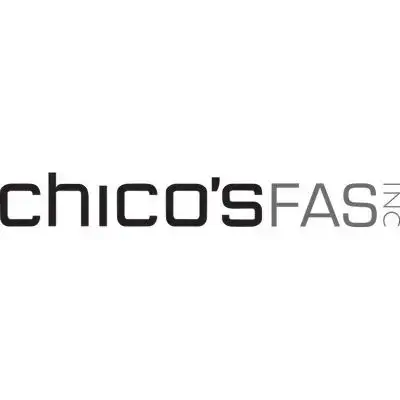
“MPulse has been with us every step of the way as our business expanded. Consistently outstanding service.”
Facilities Coordinator
Distribution Center, Chicos FAS, Inc.
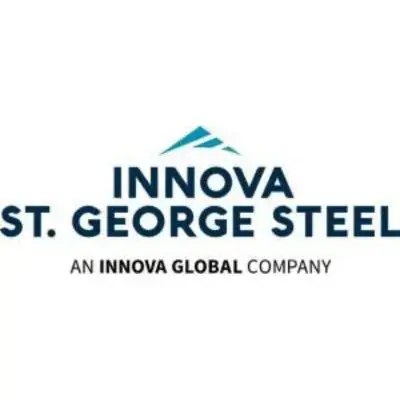
“When you use pencil and paper, it takes hours. It takes a lot of time to get a result, where it only takes minutes in software like MPulse.”
Executive Administrative Assistant
St. George Steel