MPulse CMMS Software
Streamline Maintenance Operations with Work Order Management Software
Simplify and Optimize Your Work Order Management Process with MPulse Work Order Software.
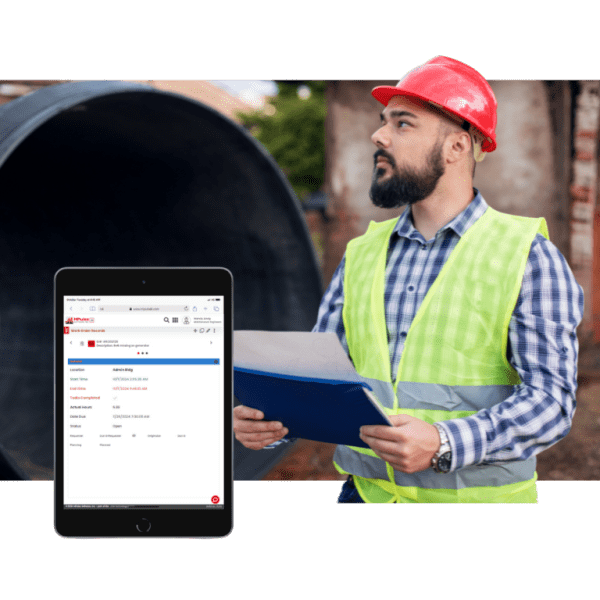
The ability to quickly locate and complete work orders is a key factor in the success of any work order management software.
The Challenges of Work Order Management
Managing work orders efficiently is crucial for maintaining smooth operations and minimizing downtime. However, manual work order management processes can be time-consuming, error-prone, and inefficient. Tracking personnel qualifications, assigning tasks based on urgency and skill requirements, and monitoring work order status can quickly become overwhelming.
Modern work order management systems ease these pain points by automating and streamlining these processes. With advanced features, work order software helps organizations track tasks in real-time, reduce errors, and improve efficiency across the board.
Start your FREE TRIAL today and experience for yourself why MPulse CMMS is the preferred preventive maintenance software for over 3,000 manufacturers and facility managers
Introducing our Work Order Management Software
The MPulse CMMS platform offers you an advanced work order management solution that is specifically designed to address pain points and streamline your maintenance operations. With its powerful features and user-friendly interface, it enables you to optimize your workflow, improve team collaboration, and ensure timely completion of work orders.
Key Features and Benefits
Track and Manage Personnel Qualifications
MPulse work order management software includes a comprehensive personnel qualification tracking system. You can effortlessly monitor employee qualifications, certifications, and training records. Say goodbye to manual tracking and ensure your team is always equipped with the right skills for the job.
Prioritize and Assign Work Orders
No more guesswork! MPulse work order management software allows you to prioritize work orders based on urgency and skill requirements. It intelligently assigns tasks to the most qualified personnel, ensuring efficient utilization of resources and reducing response times.
Real-time tracking of Work Order Status and Progress
Stay updated on the status and progress of your work orders in real time. MPulse Software is a powerful work order management system and provides a centralized dashboard that allows you to track each work order’s lifecycle, monitor completion status, and identify bottlenecks. With this level of visibility, work order systems like MPulse enable you to proactively address issues and make data-driven decisions.
Who uses MPulse Work Order Software?
Since 1995, MPulse has served more than 3,000 customers, helping them keep facilities operating at peak efficiency and manufacturing assets working at maximum productivity. Our powerful work order management systems are trusted by organizations across virtually every industry imaginable.
MPulse is designed to grow with any size business, from small organizations with one or two maintenance technicians to global enterprises with locations around the world. Our flexible work order system ensures scalability and adaptability for all types of operations. Check out how MPulse helped St. Mary’s County Public Schools.
MPulse provides work order management software to a long list of household names like Verizon, Rolex, General Dynamics, Fender Guitars, Toyota, and Siemens. Our customers are located across all 50 U.S. states and in 22 additional countries around the world.
Frequently Asked Questions About MPulse’s Work Order Software
Why Do I Need Work Order Management Software?
Organizations decide they need work order systems when whatever they’re doing stops working. We call this the “pain point.”
While a pain point differs for every organization, it typically falls into one or more of four categories: Functional, Technological, Organizational, or Scalability. If you’re struggling, there’s likely a reason.
Whatever it is, your existing system isn’t doing it well. That’s where modern work order management systems come in, addressing these challenges and improving your team’s ability to perform and track basic maintenance functions.
Learn more about identifying your pain points and how work order systems can help solve them.
What Are the "Bare Bones" Features I'll Need?
These eight features should be available in any work order management solution…
- Asset Records store details about equipment, buildings, vehicles, or other assets—asset name, purchase date, purchase price, serial number, location, and other important details.
- Employee Records store information about your employees—names, contact information, certifications, etc.
- Inventory Records record details about spare parts and consumables you have on hand—type, model, serial number, manufacturer, supplier name, location name, item number, item state, unit of measure, etc.
- Work Orders link all the elements of repair and maintenance work in one place.
- Basic Inventory Management helps you keep up with the spare parts and consumables you have on hand.
- Basic Reporting tools help you create meaningful information from the data recorded for assets, employees, inventory, schedules, and work orders.
- Preventive Maintenance Scheduling enables you to establish, monitor, and execute preventive maintenance schedules (both time- and meter-based).
- Service Requesting is essential when you get repair requests from either internal departments or outside customers—allowing users to enter and initiate service requests, and then monitor the progress of the requests as your team completes repairs.
Who Should Be Involved in the Decision?
It’s likely you need to convince other people that work order management software can help them. You’ll need to meet both their business and emotional needs if you hope to be truly successful.
In the buying process, there are several key stakeholder groups to consider:
- Users
- Senior Managers
- IT Managers
- Procurement Managers
- Financial Managers
- Legal/Compliance Officers
For each group, ask questions like…
- How is this program likely to affect each person’s daily workload positively or negatively?
- How might this program threaten each person’s job, work performance, or domain of responsibility?
- Is it possible that this person might have emotional reasons to oppose the program? What could they be?
What Are My Buying Options?
Typically, there are two ways to purchase work order management software.
Subscription pricing is also known as Software as a Service, or “SaaS.” When you opt for SaaS, you’re renting the software for a monthly or yearly fee. SaaS is a common option today—but it may not be the best one for you.
You also can purchase a license to use the software (in practical terms, forever) for a one-time fee. Typically, you will also have the option of purchasing or renewing a yearly maintenance agreement that includes software updates, tech support, hosting services, and access to training. It’s usually charged as a percentage of the software’s original price.
How Many Software Licenses Do I Need?
Traditionally, work order software is sold as a per-seat license. You’ve probably been buying software this way since your first computer. Imagine an office with 30 people. Under the per-seat license model, you’d buy 30 licenses, so each user can access the software. If you hire a new person, you need to buy another license.
Concurrent licensing is a newer approach with the potential to save you money. The number of concurrent licenses you need is based on the number of users accessing the software at the same time.
Let’s take that same office with the same 30 people. You have 18 people on the day shift—10 technicians, three parts room employees, two admin assistants, one foreman, you, and your boss. On the night shift, you have another 10 technicians, one parts room employee, and one foreman.
Because not all users will be accessing the system at the same time, you can reduce the number of licenses you need by more than a third. So you’re not paying extra for users who use the software at different times or only need access occasionally.
Here’s how to calculate the number of software licenses you need.
Preventive maintenance involves regular, scheduled upkeep to prevent equipment failures before they occur. It reduces unexpected breakdowns, extends the lifespan of assets, and lowers overall maintenance costs. A CMMS makes implementing preventive maintenance easier by automating schedules and tracking work history.
Learn how you can ensure your success with preventive maintenance software.
What if I Need to Integrate with My Organization’s Other Software?
Organizations decide they need work order systems when their current processes stop working effectively. We call this the “pain point.”
While a pain point differs for every organization, it typically falls into one or more of four categories: Functional, Technological, Organizational, or Scalability. If you’re struggling, there’s likely a reason—and it’s often tied to the limitations of outdated work order systems.
Whatever the issue, your existing system isn’t doing it well. That’s where modern work order systems come in, addressing these challenges and improving your team’s ability to perform and track essential maintenance functions with greater efficiency.
Learn more about identifying your pain points and how work order management systems can help solve them, ensuring smoother operations and reduced downtime.
What if I Need Support after the Software is Up and Running?
If you’ve ever worked with outdated software, you understand the dread when there’s a glitch and you don’t have access to technical and usability support. You usually end up paying for updates and services as you go. It’s inefficient—and expensive.
Work order management software needs its own preventive maintenance to keep it functioning properly—just like any asset. Service updates, software maintenance, and support programs help.
Software maintenance support varies by vendor, so ask questions during your initial research. Not all software support is equal. While we can’t claim to know how other vendors’ support programs work, we can share our program so you understand why it’s so important.
Learn why 90% of our customers renew their MPulse Maintenance and Support Program every year.
What if My Needs Change?
It’s not uncommon for maintenance managers to need more advanced features later or need to expand their work order management software to new locations as their organization grows. You want a way to implement CMMS software upgrades without having to start from scratch.
Scalable software keeps you on top of the increased workload—more equipment, additional production, new staff members, extra inventory, different safety procedures, etc.
From a business standpoint, software scalability is cost effective because you can buy what you need when you need it. You can’t always predict these changes, yet software scalability ensures you are prepared when they happen.
MPulse Means Happy Customers
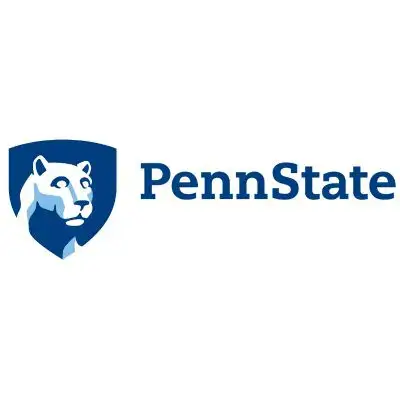
“The features and price made MPulse the right choice and the service has been excellent.”
John Smith
Maintenance Supervisor, Penn State University
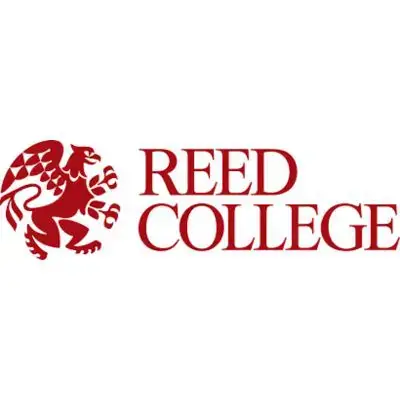
“You can tailor the program to fit the needs of your particular facility. The performance of the software is overall very good.”
Maintenance Manager
Reed College
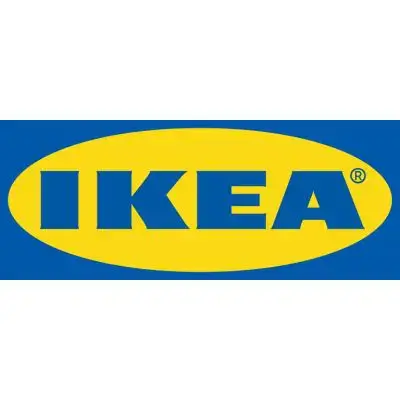
“I started using MPulse in March of 2006 using v6. The upgrade to v7 has been a smooth and easy transition offering more of the features that are needed by my sites.”
Facilities Manager
IKEA US West Inc.
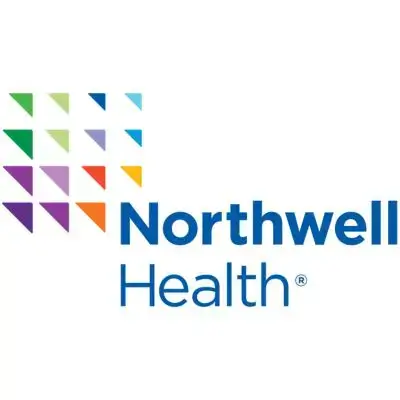
“It certainly has simplified keeping track of what we do and how we do it.”
Director of Engineering
Real Estate Services, Northwell Health
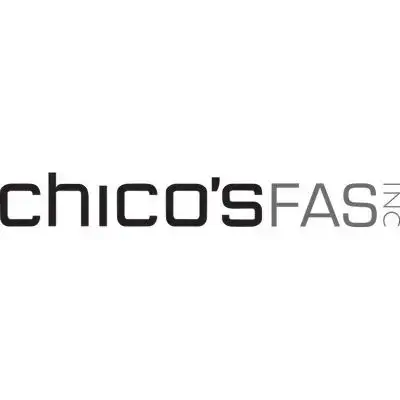
“MPulse has been with us every step of the way as our business expanded. Consistently outstanding service.”
Facilities Coordinator
Distribution Center, Chicos FAS, Inc.
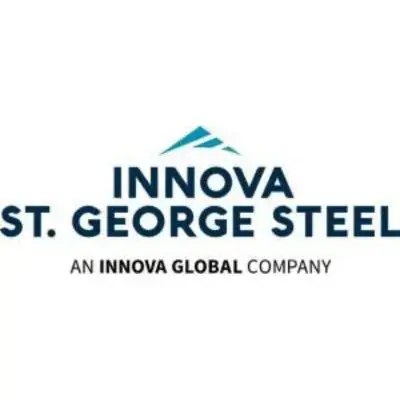
“When you use pencil and paper, it takes hours. It takes a lot of time to get a result, where it only takes minutes in software like MPulse.”
Executive Administrative Assistant
St. George Steel
Ready to Streamline Your Work Order Management?
Take control of your maintenance operations today with our industry-leading Work Order Software. Experience the power of automation, collaboration, and real-time visibility. Start your free trial now!